MATERIALS for IDEAS
REALIZE IDEAS
Today Composite components allow you to think in dimensions which still were unimaginable some years ago. Fiber compounds and its excellent abilities meet us in many situations in everydays life and accelerated and influenced the technical developments extremely. If aircraft construction, automotive industry, medical technics, sports or leisure, there is nearly no field where the advantages and possibilities of composites don’t take effect.
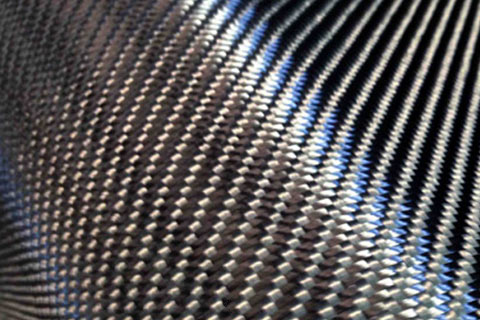
SURVEY OF PROCESSES
LFI LONG FIBER INJECTION MOULDING WITH REACTIVE PU
PROCESS
Glass fiber rovings are cut at the mixing head directly and then brought in the open tool together with polyurethane. The hardening happens in the closed tool.
MAIN ADVANTAGE
Light components with high impact strength not only in automotive industry
ADVANTAGES
High quality surfaces by simple process combinations (IMP, foil)
High strength values (fiber portion till 50 percent, fiber length 12,5 – 100 mm)
Moderate tool- and installation cost
CHARACTERISTICS
Fiber content and length locally adjustable
Easy integration of inserts (e.g. inserts and fixing elements)
Favourable basic materials, minimum fiber waste
Characteristic profile similar to SMC at lower weight
APPLICATION FIELDS
Hoods, roof elements, side coverings, coverings, flaps, dash boards
ANNUAL QUANTITIES
10.000 to 120.000 pieces
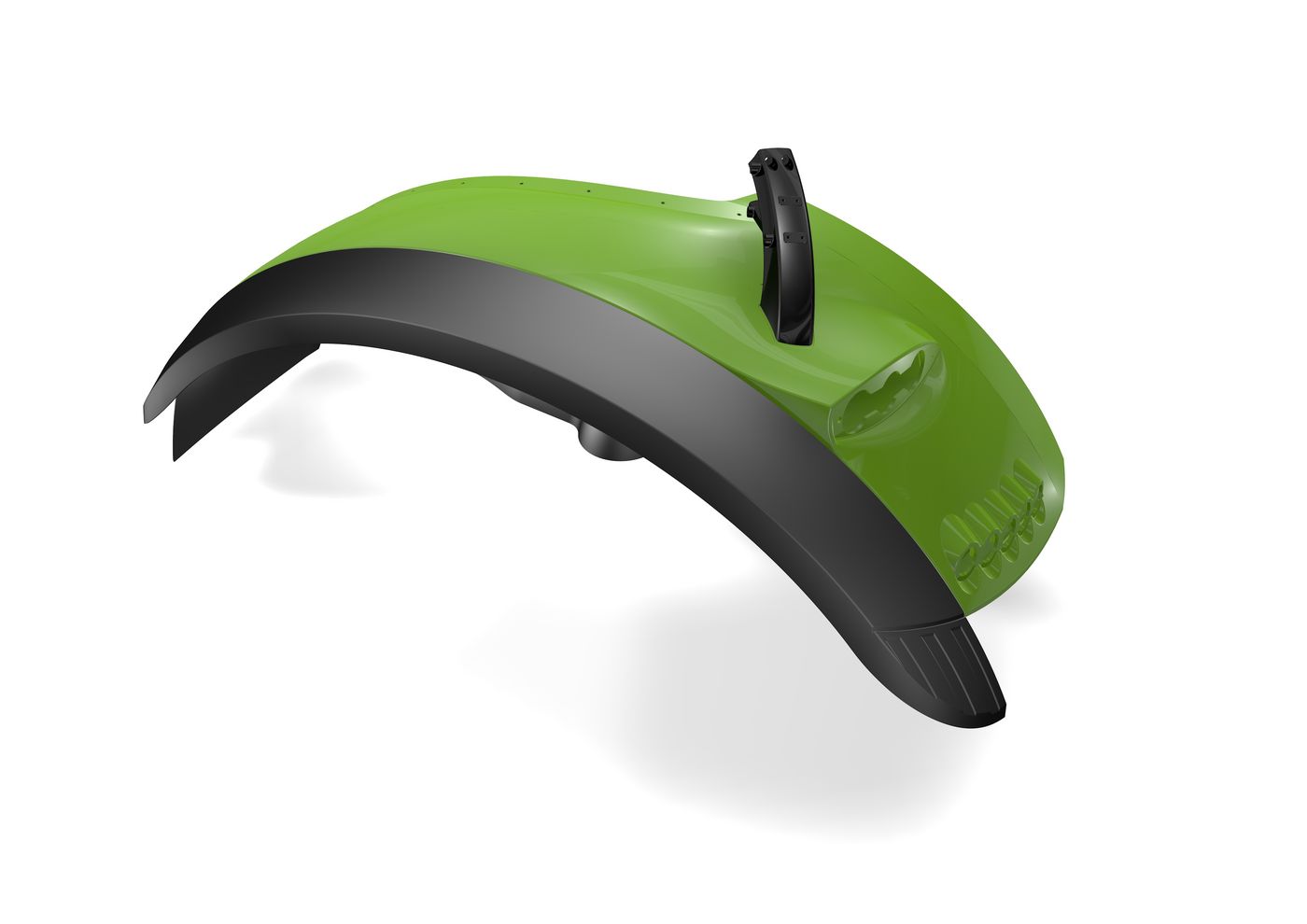
PRODUCT
LFI-ROVING MULTISTAR® 576
Advantages: suitable for highspeed working, dust reduced cutting behaviour. PU size for very good fiber-matrix-adhesion
Packing: Splicing on clients request
The LFI process is a continuous process with heavy demands on the used raw materials. Here the glass fiber roving is of great importance: With partly very high speed the roving strain is guided to the cutting device by tubes and hereby it must maintain its compact shape. The cutting device determines different fiber lengths but also the fiber content. Supposition is here a very good cutting ability of the roving.
But it shouldn’t be „too hard“ and so cause negative endurance of the cutting tools. After cutting the roving strain must disperse in its single filaments in the air stream.
Lumping, so-called „snow balls“, or filament dust can block this process resp. pollute the surfaces of the surroundings. Instead of this the roving strain should decompose most homogenous so that it can be brought in the open tool in a focused atomizing cone in exact position and reproducible.
Because of the very short process cycles glass fibers further must interlace extremely fast with the PU, to achieve the high mechanical strength of the component. Corresponding PU-components in the size enforce this cross linkage.
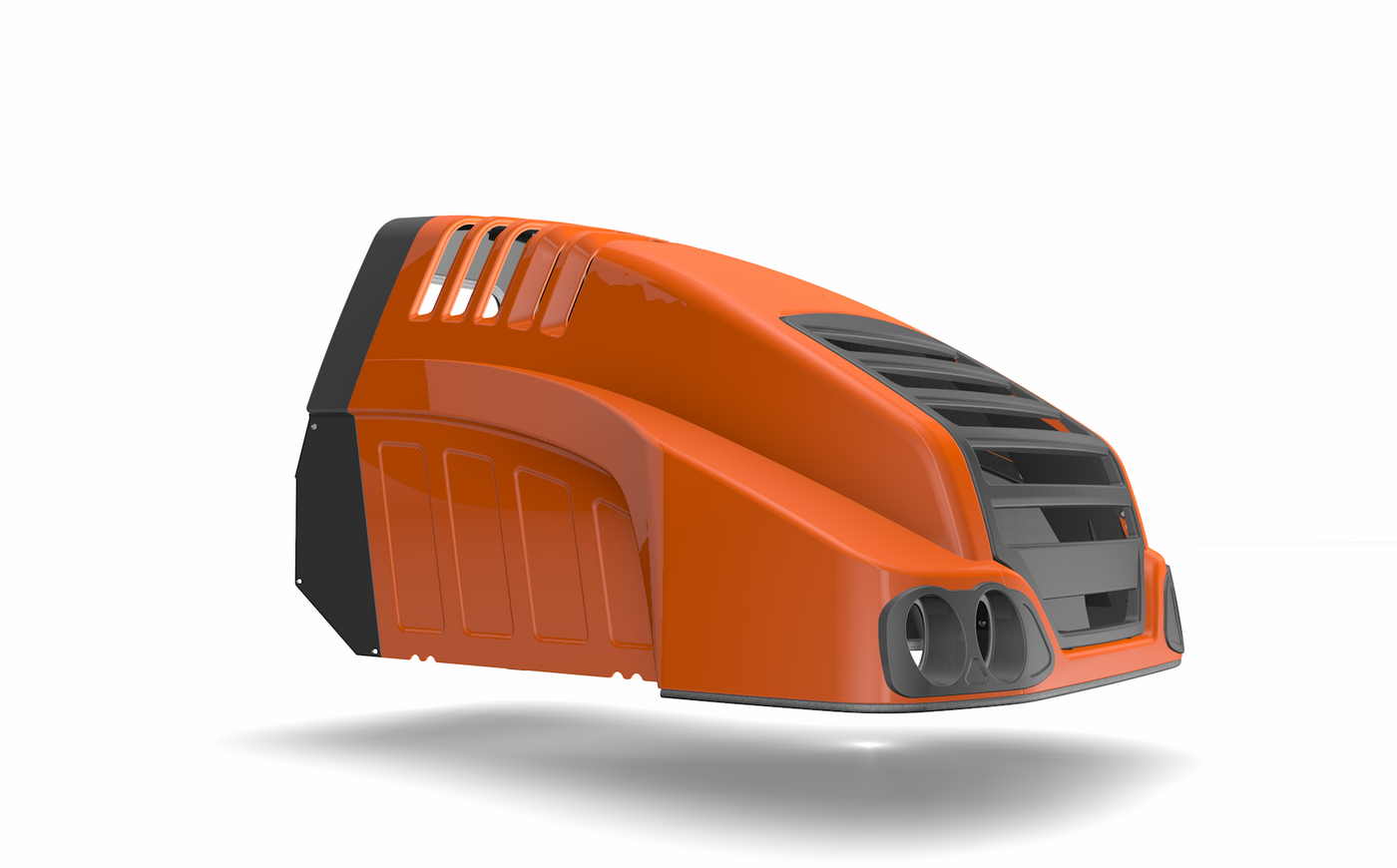
PU-SANDWICH BAYPREG® / SCS WITH REACTIVE PU
PROCESS
A prefabricated sandwich of chopped strand mat/cardboard comb core/chopped strand mat is sprayed with PU mixture and deposited in the tool; shaping and hardening in the closed tool.
MAIN ADVANTAGE
Low component weight at high flexural- and compression strength
ADVANTAGES
Optimized light construction for moderate strength
Low operating cost, low material consumption
On both sides high quality finish surfaces possible
CHARACTERISTICS
On both sides spray of fibermat in a fixing frame
Simple combination with surface decoration in the tool
Light components with comb core
APPLICATION FIELDS
Hat racks, loading floors, laminated extensive components, sliding roof
ANNUAL QUANTITIES
10.000 to 300.000 pieces
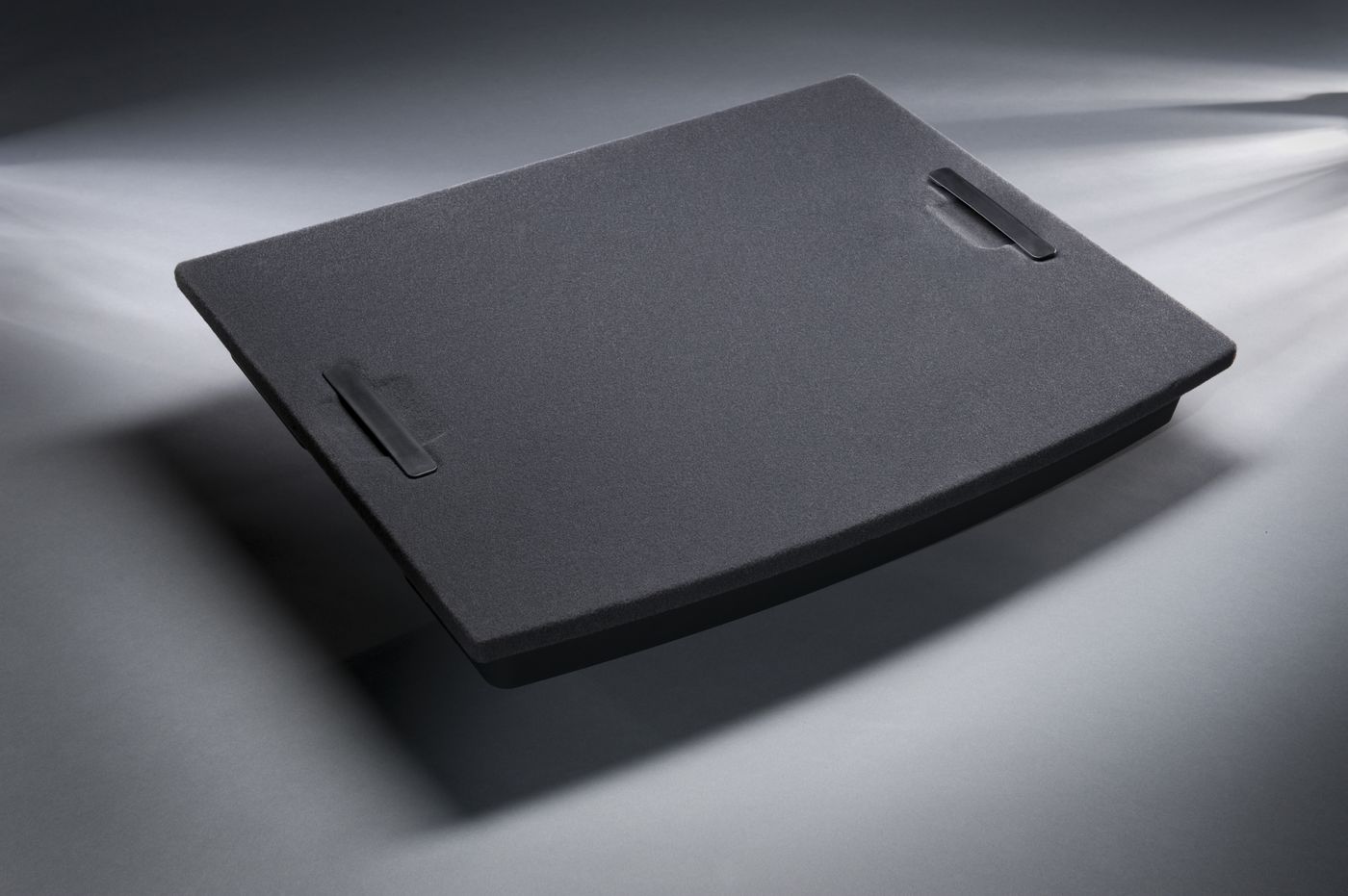
PRODUCT
CSM-FI AUTOMOTIVE / CSM AUTOMOTIVE PU AND EM / ALL CSM-PRODUCTS / NEEDLE MAT
SM-FI AUTOMOTIVE: highly fine fiber filaments, from 100 g/m², powder bound
CSM AUTOMOTIVE PU AND EM: powder- or emulsion bound, from 225 to 900 g/m², for PU optimized size.
ALL CSM-PRODUCTS: low tolerances in basis weight and binder content, exact edges, big bobbins on client’s request, proportionated fiber face from the very beginning, width from 10 to 360 cm, high mechanical dry strength, optimized for automized processes, big rolls to 1000
NEEDLE MAT: binder free mat, stretchable, for strong outlines and crimps
An automized produced sandwich construction where the fiber mats with a high dry strength lay outside on a cardboard comb core, is sprayed with non-reinforced PU on both sides. Then the sprayed sandwich will be laid into the tool which then will be closed. A very proportionated fiber distribution is supposition for a fast matrix distribution and later homogenous surface of the moulded part. The fiber mats will be impregnated with PU whilst pressing process and whilst hardening the mats glue together with the fiber core. Binder, optimized for PU, care for a fast fiber/matrix adhesion and high mechanical strength.
Considering the material characteristics and the geometry extremely light components with extremely high flexural- and compression strength are created with harmonized supporting- and core layers.
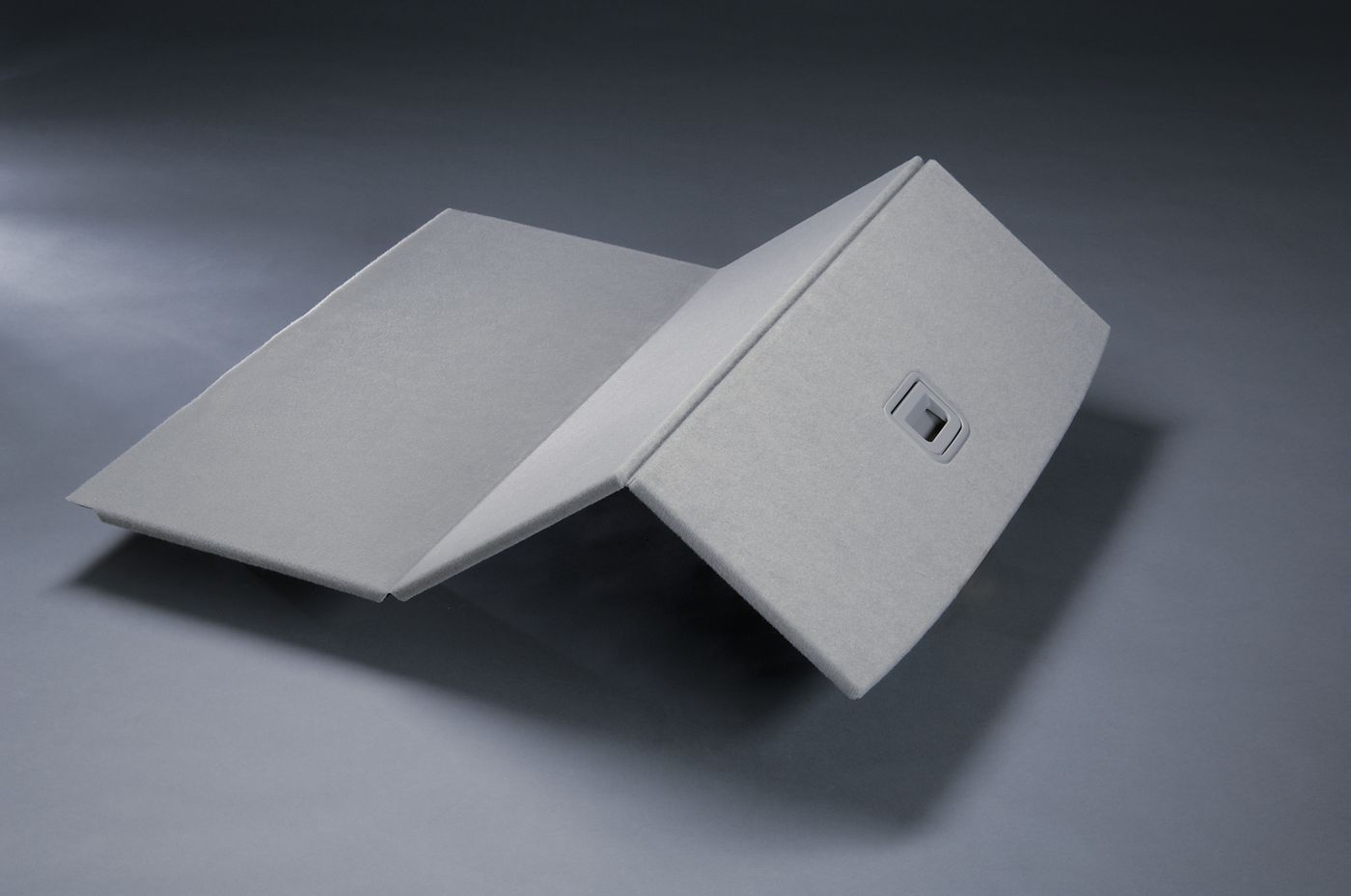
RTM AND RTM LIGHT - RESIN TRANSFER MOLDING
PROCESS
RTM: unsaturated fiber mats or multi layer fabrics are injected with resin in the closed mould.
RTM LIGHT: stands for a low pressure injection with additional vacuum support
MAIN ADVANTAGE
Highly strength structure components for individual applications
ADVANTAGES
Optimized mechanical strength
Professional high quality finish, class-A-surfaces
Good reproducibility
Moderate investment in installation- and mould construction
Production of small series
Uniform wall thickness
Lighter components than in hand process
CHARCATERISTICS
Ideal for small and middle series
More proportionated production compared with hand laminate
APPLICATION FIELDS
Motor sports, individual buildings, architecture
ANNUAL QUANTITIES
Up to 100 pieces
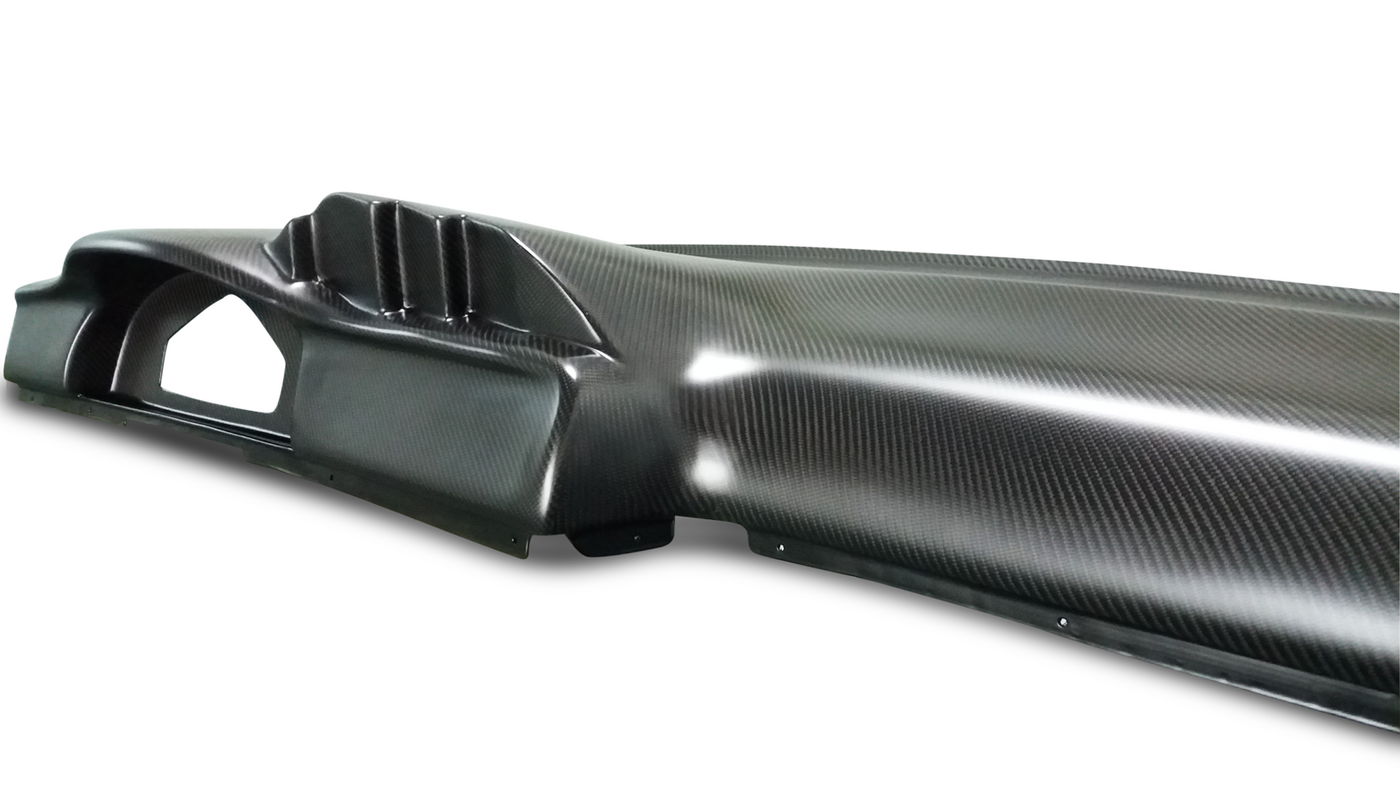
PRODUCT
EPOXY RESINS / POLYESTER RESINS / FABRICS OF GLASS- AND CARBON FIBERS
EPOXY RESINS: with component optimized viscosity and reactivity, highly transparent, UV-resistant
POLYESTER RESINS: on orthophtalic or isophthalic base, low viscous and styrene poor, also suitable for fire protection (halogenous free)
FABRICS: of glass- and carbon fibers (also unidirectional)
MULTI LAYER FABRICS: uni- or multiaxial of glass- and carbon fibers
NONWOVENS: for class-A surfaces
3D-CORE: tridimensional drapable core material
FLOW AIDS / DISTANCE SUPPORT: like textile knitted fabrics and nonwovens of glass fiber, PP and PES
Unsaturated reinforcing fibers eventually in form of pre-ready made and outline near preforms will be laid into the tool. After closing the mould the reactive resin system will be injected and flows through the fiber layers. After impregnation excess resin flows out at the ventilation.
Mostly the matrix consists of duroplastic plastics like polyester, epoxy- or phenol resin.
Using high reactive resin systems it’s possible to reduce the cross linkage time under 3 minutes and to realize so short cycle times in RTM-process.
As fibers are used glass fibers, carbon fibers and also fibers of polymer materials like aramid- and polyethylene fibers. Hereby the fiber rovings can be worked to different fiber half-finished goods with different architecture.
Besides multi layer fabrics, fabrics, nonwovens and mats also knitted fabrics and plaitings are used for the production of components of fiber reinforced plastics.
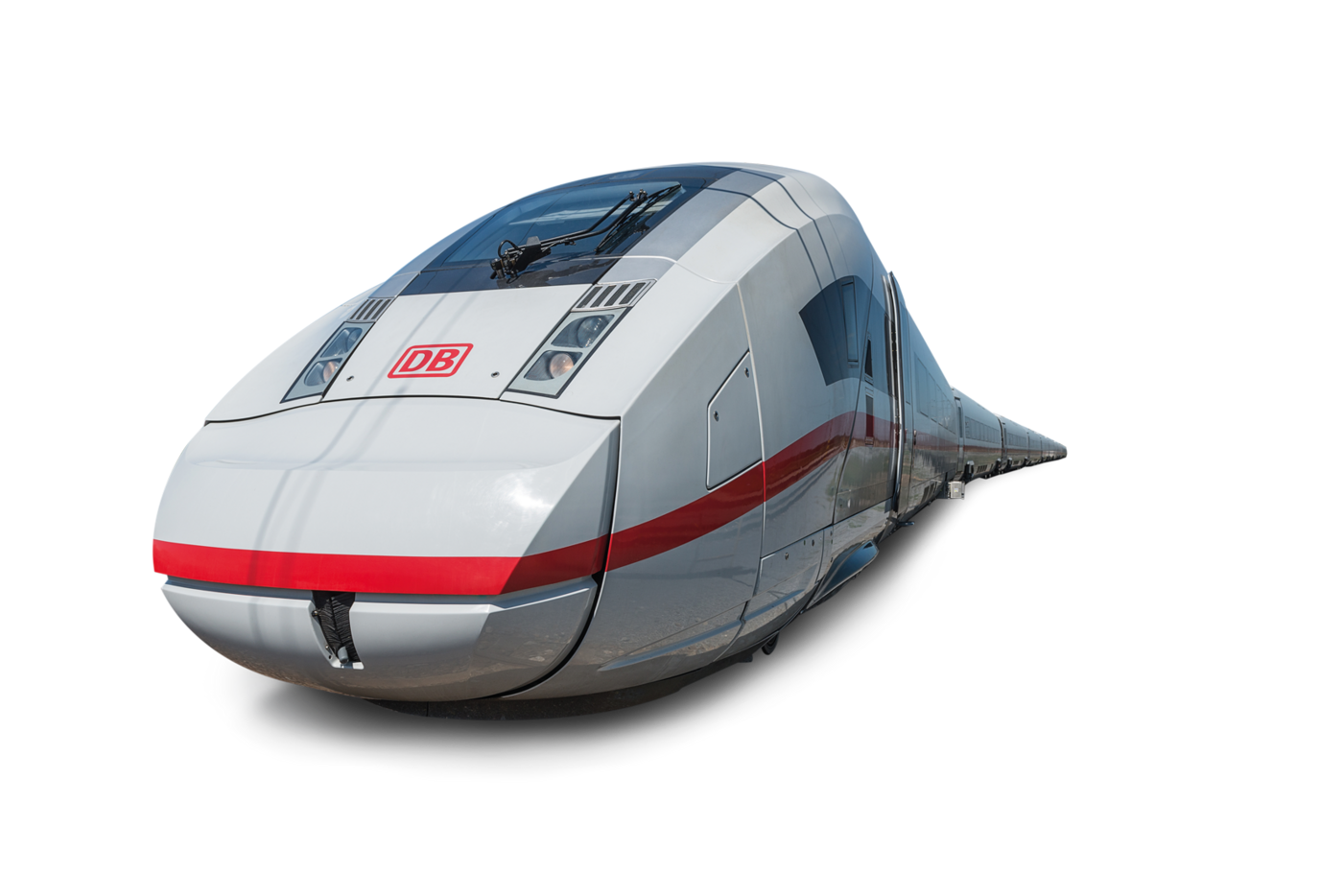
HD-RTM / C-RTM HIGH PRESSURE / COMPRESSION RESIN TRANSFER MOLDING
PROCESS
HD-RTM: Pre ready-made fiber mats or fabrics will be laid into the tool. After closing happens the resin addition and the reaction in the closed tool.
C-RTM: Fiber mats and fabrics will be laid into the tool. Resin addition happens in the tool that is opened a slit and the reaction then in the closed tool.
MAIN ADVANTAGE
Very light, highly strong high-performance-light components
ADVANTAGES
Light components for highest requirements. Ca. 50% more light than steel
Visible components with high quality carbon optics
Components which can be varnished for visible applications
Full automation possible and suitable for series production (from pre-form manufacturing till rework)
CHARACTERISTICS
Nearly unidirectional reinforcements with continuous fibers possible
High pressure technics allow the use of fast reacting systems
High fiber portions of up to 50 percent
APPLICATION FIELDS
Structure components, side walls, both tubes, bumpers, crash boxes, carbon design parts
ANNUAL QUANTITIES
10.000 to 120.000 pieces
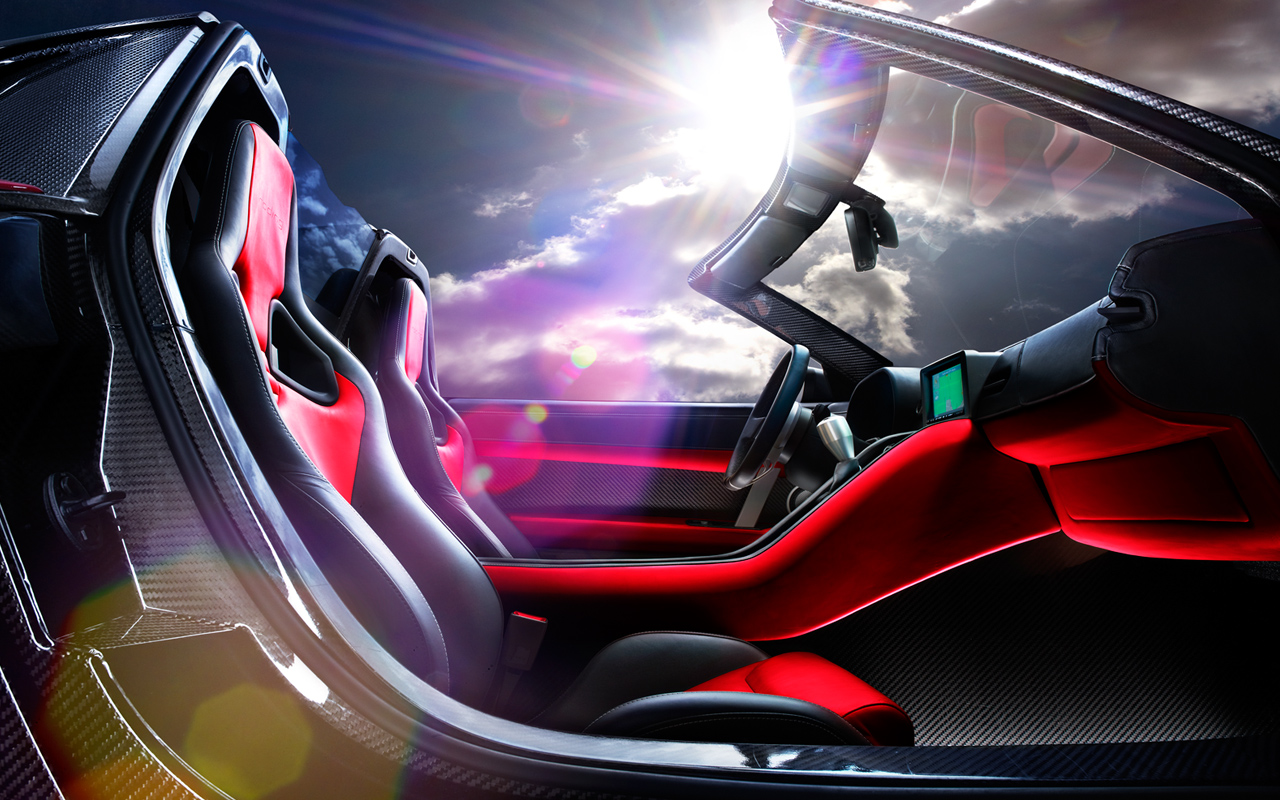
PRODUCT
FABRIC AND MULTI LAYER FABRICS OF GLASS- AND CARBON FIBERS / NONWOVENS FOR CLASS A SURFACES
FABRIC: of glass- and carbon fibers for thermo- and duroplast matrix (also unidirectional)
MULTI LAYER FABRIC: uni- or multiaxial of glass- and carbon fibers
NONWOVENS: for class A surface
FLOW AIDS / DISTANCE SUPPORT: like textile knitted fabrics and nonwovens of glass fiber, PP and PES
In HD-RTM-process [high pressure resin transfer molding] a fiber preform of glass- and/or carbon fibers will be built up. The composition happens orientated on the demand corresponding to the load of the later structure component. This preform will be laid into the tool, which will be closed and evacuated then. After that a very low viscous, reactive epoxy resin, polyurethane or cast polyamide will be injected into the cavity to moisten so each single fiber without air inclusions.
The C-RTM process (Compression Resin Transfer Molding) mainly differs from HD-RTM process, that the resin mixture will not be put into the closed but into the tool with open gap. This means that the tool isn’t closed completely whilst filling. So the preform already becomes partly perfused with resin. After filling happens a compression lifting which causes that the resin will be pressed through the preform and so becomes perfused completely.
Excellent strength: In HD-RTM process extremely light structure components for highest requirements are realized that appear for example in automobile crash tests. It’s already established in the aerospace industry, in engineering industry and in automobile industry. In HD-RTM process fiber contents of 50 percent are achieved.
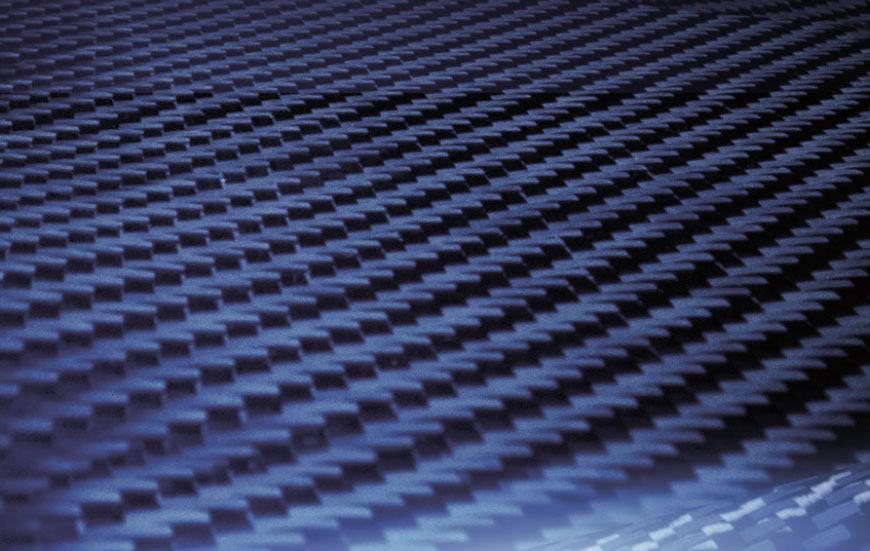
HOT PRESS AND AUTOCLAVE PROCESS OF PREPREGS
PROCESS
Prepreg is the short form of „Pre-impregnated Fibres“, so with epoxy- or phenol resin pre-saturated fabrics and multi layer fabrices out of carbon-, glass-, aramid- or hybride fibers. Different prepreg systems are existing depending on process and use. The prepregs will be inserted into the mould and wrapped with punched foil, suction nonwoven and foil before these are pressed under vacuum or in autoclave.
MAIN ADVANTAGE
Calculable components with an optimum component weight at maximum strength
ADVANTAGES
Process security
Short cycle times
Dimsensionable fiber volume and component weight
Clean working
Minimum danger of allergy
CHARACTERISTICS
Defined and so optimzed fiber-/resin portion
Very good strength values at extremely light weight
Uniform wall thickness
Low ondulation and high fiber volume portion
APPLICATION FIELDS
Aerospace, automotive, engineering industry, industrial components and production of heavy duty sports equipment.
ANNUAL QUANTITIES
From 10 pieces (e.g. prototype construction) till 1.000 pieces in series production
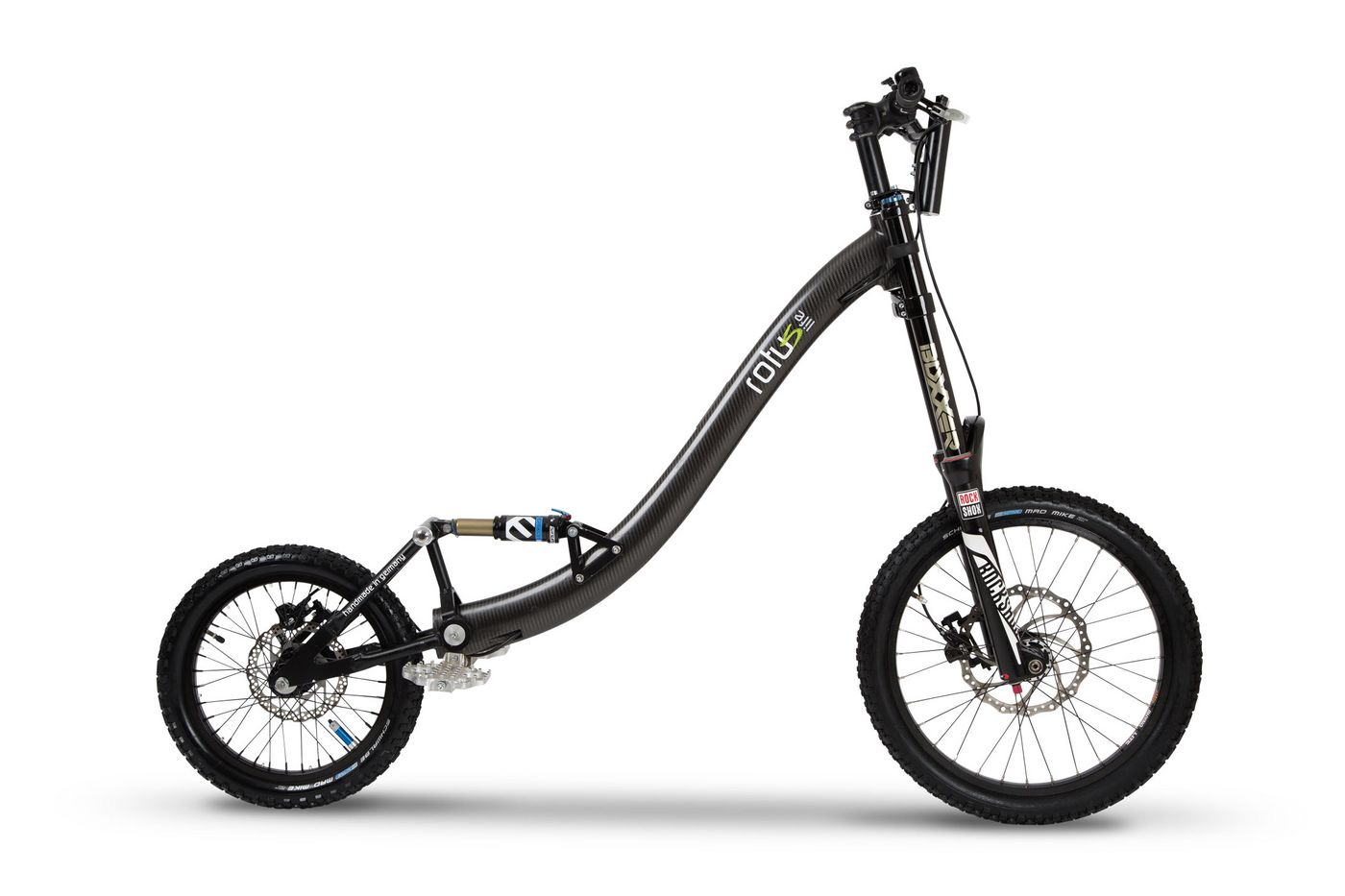
PRODUCT
PREPREG / 3D-CORE / NONWOVEN FABRICS
PREPREG: for all processes
3D-CORE: tridimensional drapable core material
NONWOVENS: for Class A surfaces
Pre-saturated fabrics will be laid into the mould / the tool. Then separating-/punched foil and suction nonwoven will be laid on the prepreg that excess resin can be sucked off under pressure of 1 bar – 30 bar (depending on application). As moulds normally carbon- (e.g. produced of special tooling prepreg) or steel pressing moulds are used. Depending on the requirements to the component or the processes different prepreg systems are used:
Low temperature prepregs: Working at a pressure till 1 bar and temperatures from 75°C
Autoclave- and hot press prepregs: Working larger than 1 bar - 20 bar and at temperatures from 80° C to 180° C depending on the application field. In hot press process no foils or suction fabrics are used.
Tooling prepregs: Working in the autoclave from 2 bar to 30 bar and temperatures from 120°C to 200° C.
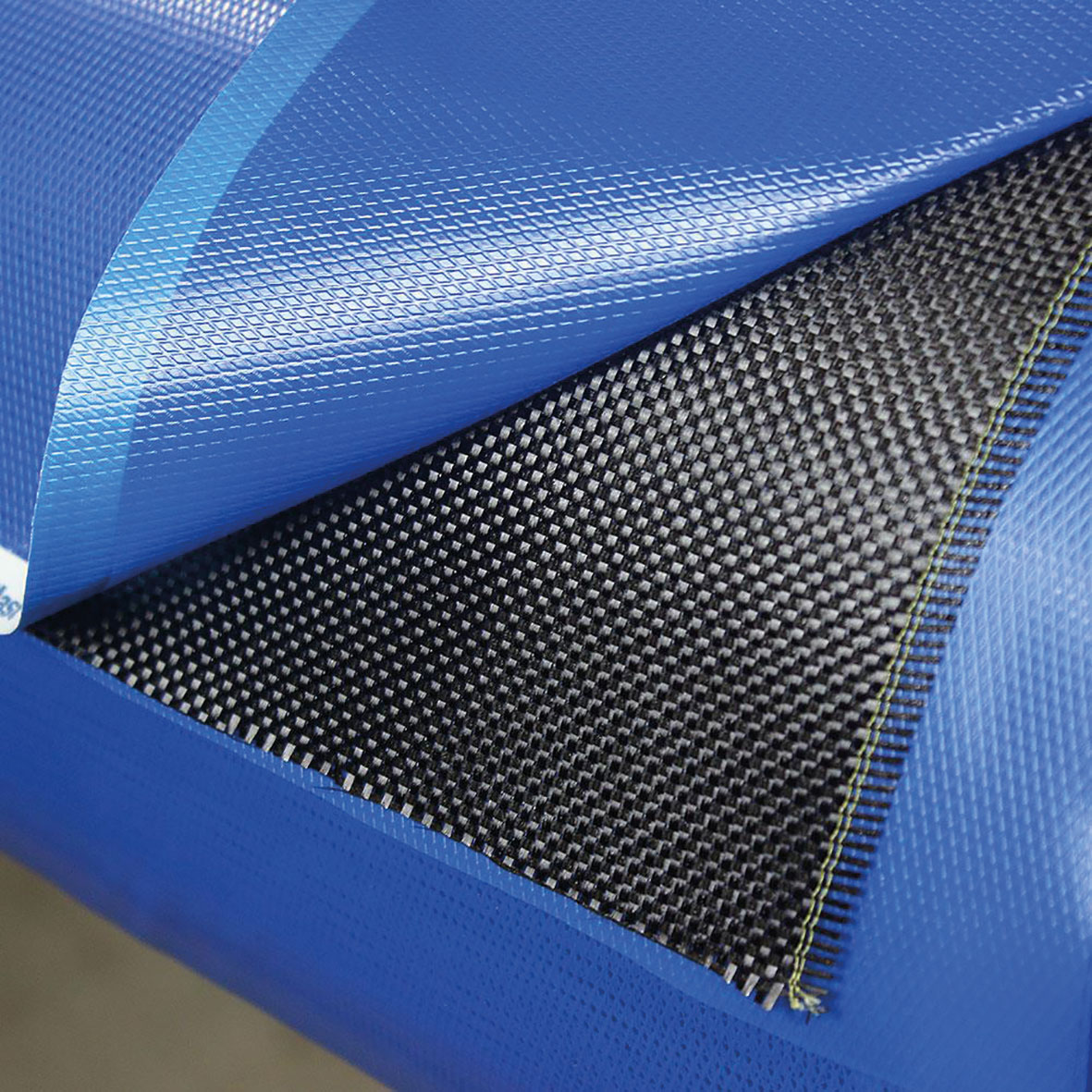
FIBER WINDING / PULTRUSION
PROCESS
In pultrusion process fiber glass rovings are torn into moulding tools which are tempered.
MAIN ADVANTAGES
Tanks and tubes for modern driving technics
ADVANTAGES
Essential weight advantage compared to steel
Corrosion- and UV protection
CHARACTERISTICS
High design freedom
Till 80MPa internal pressure
Low production costs
APPLICATION FIELDS
High pressure gas container for natural gas drivings, primary shafts, plate springs
ANNUAL QUANTITIES
10.000 to 120.000 pieces
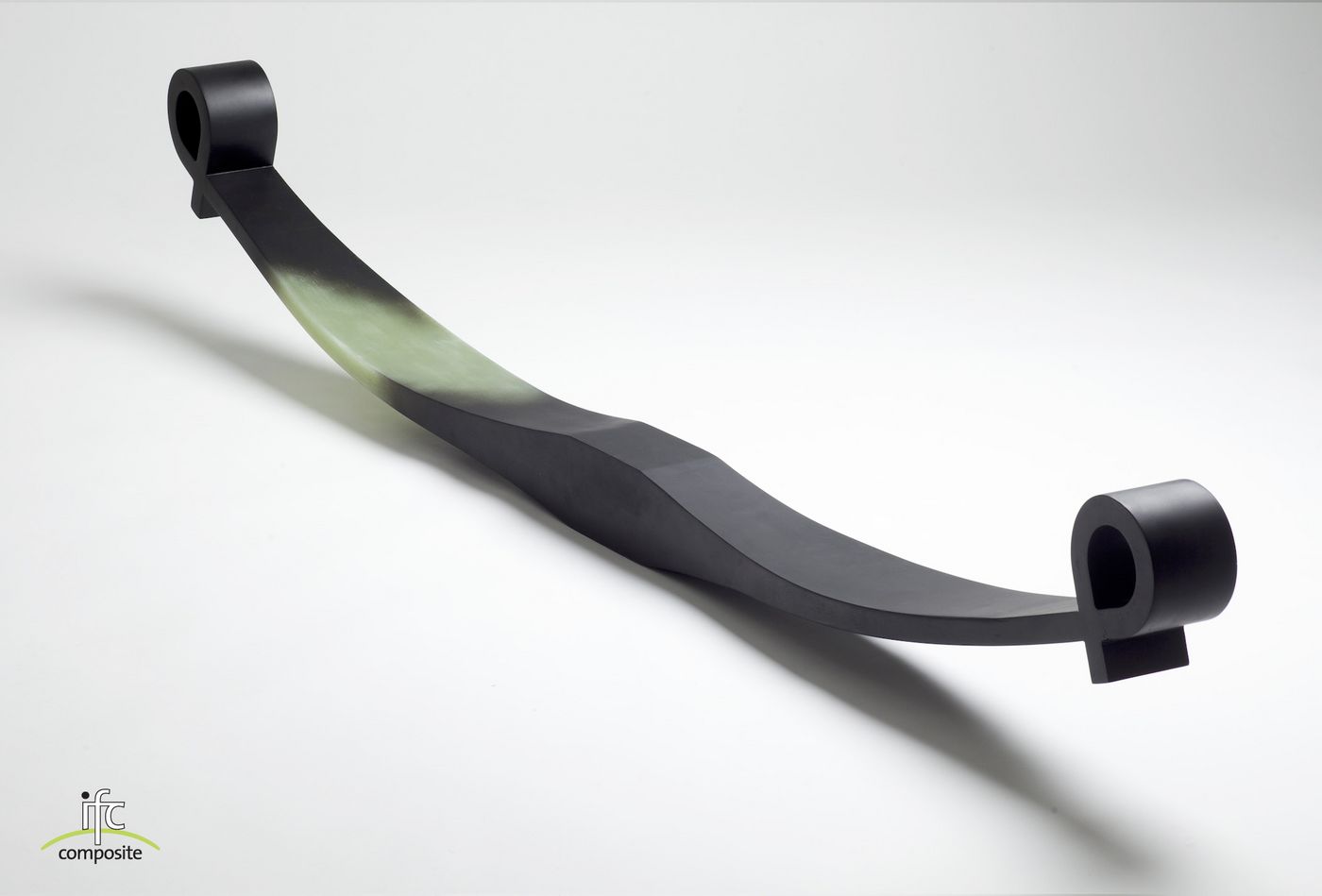
PRODUCT
EPOXY RESINS / POLYESTER RESIN / STARROV® 086 / STARROV® 908 / ECR-ROVINGS / NONWOVENS
EPOXY RESINS: with component optimized viscosity and reactivity, highly transparent, UV-resistant
POLYESTER RESINS: on orthophtalic or isophtalic base, low viscous and poor of stryrene, also for fire protection (halogenous free)
STARROV® 086: for UP-, EP- and VE-resins, very soft silane size, nearly free of fluffs
STARROV® 908: for UP-, EP- and VE-resins, stress free draw off, fast perfusion
ECR-ROVINGS: for application in corrosive surroundings
NONWOVENS: of E- and ECR-glass, to protect surfaces from corrosion
In open pultrusion processes the fiber rovings are led into a resin bath or the impregnation installation. The fibers pass several preform stations, so that they are led to the requested profile shape. Mats, fabrics, multi layer fabrics or nonwovens can be integrated in the process at the fiber guidances to adapt resp. to optimize the mechanical characteristics against a pure unidirectional reinforcement as it’s achieved by fibers.
At the so-called closed process all the reinforcing fibers only get in contact with the unhardened monomers in the moulding tool, but then with increased pressure for a better impregnation. In the tool the monomer reacts to the polymer. The hardened semifinished products is be pulled through a caterpillar haul-off and so also pulls on the fibers along with the matrix.
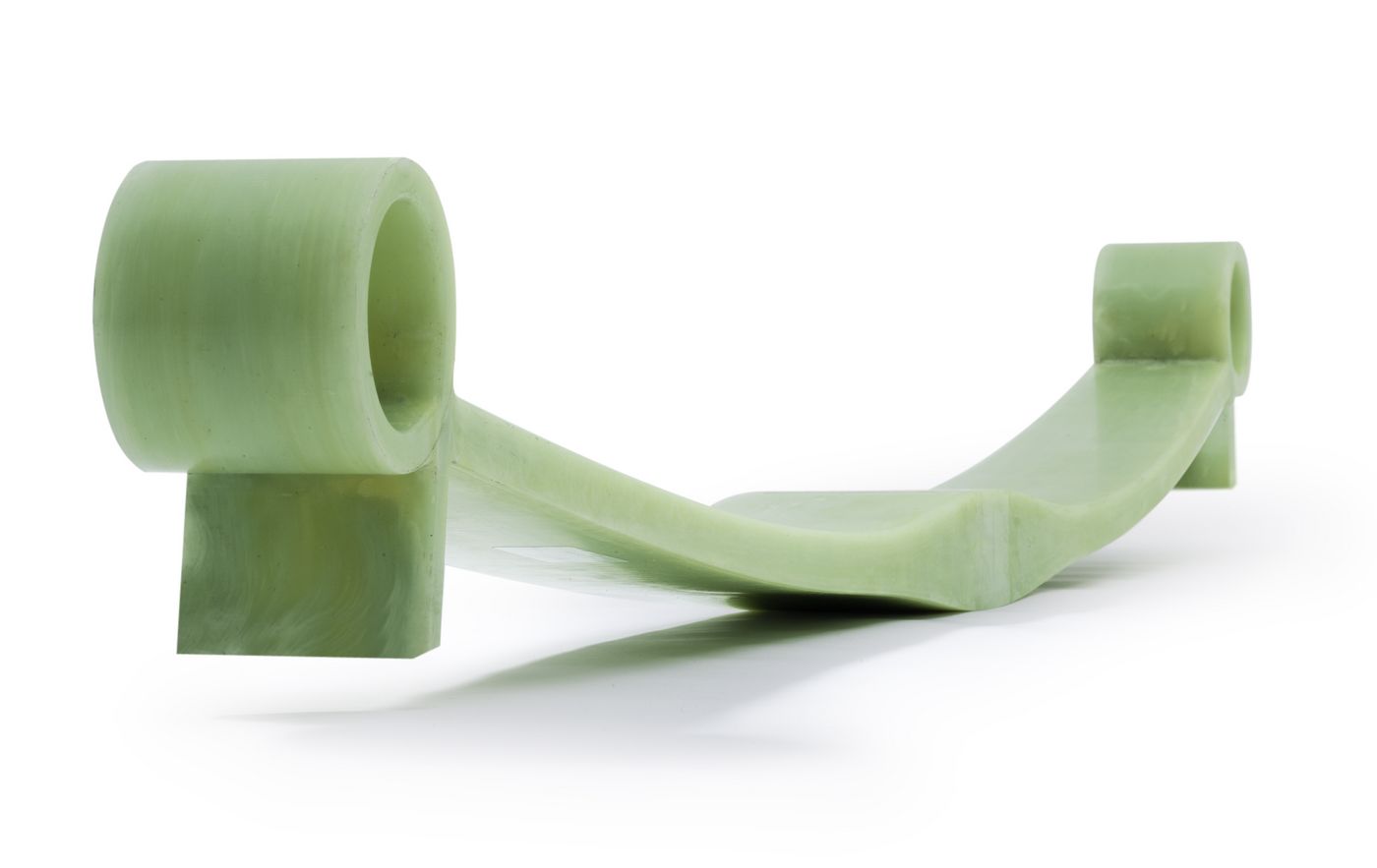
INJECTION MOULDING (LFT) SHORT- AND LONG GLASS FIBER REINFORCED THERMOPLASTS
PROCESS
Many thermoplast granulates for injection moulding machines are reinfored with short chopped glass fibers to increase the mechanical charactistics clearly. In LFT process with fiber lengths up to 25 mm still much higher mechanical characteristic values are achieved.
MAIN ADVANTAGES
Injection moulding for fiber reinforced compounds
ADVANTAGES
Short cycle times allow a full automatic production of high piece numbers
By fiber portion improved meachnical characteristics and high rigidity
Combinable with nearly all variants of injection moulding process
CHARACTERISTICS
With light modifications standard injection moulding machines can made fully automatic
Working and process are well-known
Recompound utilization
APPLICATION FIELDS
Seats, dashboards, door modules, technical parts in the motor room
ANNUAL QUANTITIES
300.000 to 600.000 pieces
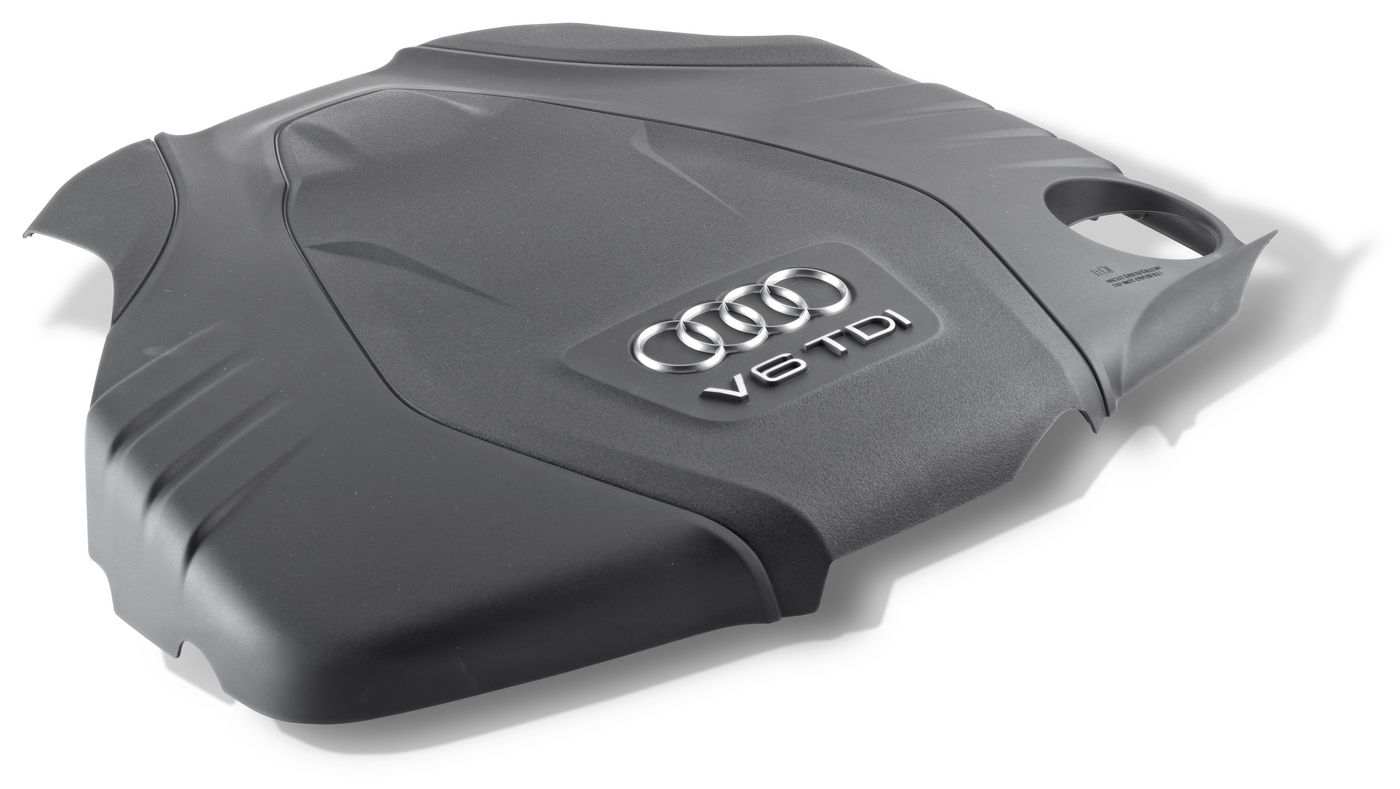
PRODUCT
ALL THERMFLOW®-FIBERS / STARROV® 490 / TECHSPHERES / TECHBEADS
THERMOFLOW® 672: for PA and PA 6.6: maximum tensile- and impact strength; no drop of nominal values with stearates
THERMOFLOW® 675: for hydrolysis resistant PA
THERMOFLOW® 636: for PP: best mechanical and dynamical values, suitable for uncoupled PP
THERMOFLOW® 601: for POM, PBT, PC and PF
THERMOFLOW® 768: for high temperature polymeres PEEK, PES, PPS, PEI a.o. ALL
THERMOFLOW®-FIBERS: directly chopped fibers, very good dosage, high apparent density, neutral colour in the compound, Big Bag and Oktabine-packaging
STARROV® 490: for LFT PP
TECHSPHERES / TECHBEADS: Microglass balls with silane coupling agent
To achieve a higher component rigidity, many technical thermoplasts like PA, PP a.s.o. are reinforced by short cut glass fibers which are especially modified for the respective matrix. The compounds ready for working normally have a fiber portion of 15 to 50 weight percent, but supposition is that the fibers have good pourability and so can be dosed exactly. Further client-specific requirements like hydrolysis- or high temperature resistance are special characteristics of glass fibers for thermoplast reinforcement.
All this also can be achieved with longfiber reinforced thermoplast granulate (LFT) at lower fiber content and so lower weight. The length of the fibers corresponds to the granulate length, common are fiber lengths of 12 and 25 mm. LFT with higher fiber portion are preferred used for non-visible semi-structure components like frontends and dashboards. These components require a high impact strength, to bear also vibrations and shocks. On principle LFT components have less fiber orientation, since the long fibers are blocking each other.
DIRECT-COMPOUNDING (D-LFT)
PROCESS
The D-LFT process connects the continuous compounding of extrusion technics with the discontinuous injection moulding. So longfiber reinforced thermoplast components with better characteristics can be produced less expensive than from granulate.
MAIN ADVANTAGE
D-LFT combines compunding and injection moulding – ideal for bulk series
ADVANTAGES
Short cycle times allow the full automatic production of high piece numbers
Improved mechanical characteristics and high rigidity by long fibers
Favourable material cost
CHARACTERISTICS
Process highly to automate
Flexible adjustable on requirements
Material mixture of favourable standard raw materials
APPLICATION FIELDS
Frontend carrier, gear carrier, spray walls, battery tank
ANNUAL QUANTITIES
300.000 to 600.000 pieces
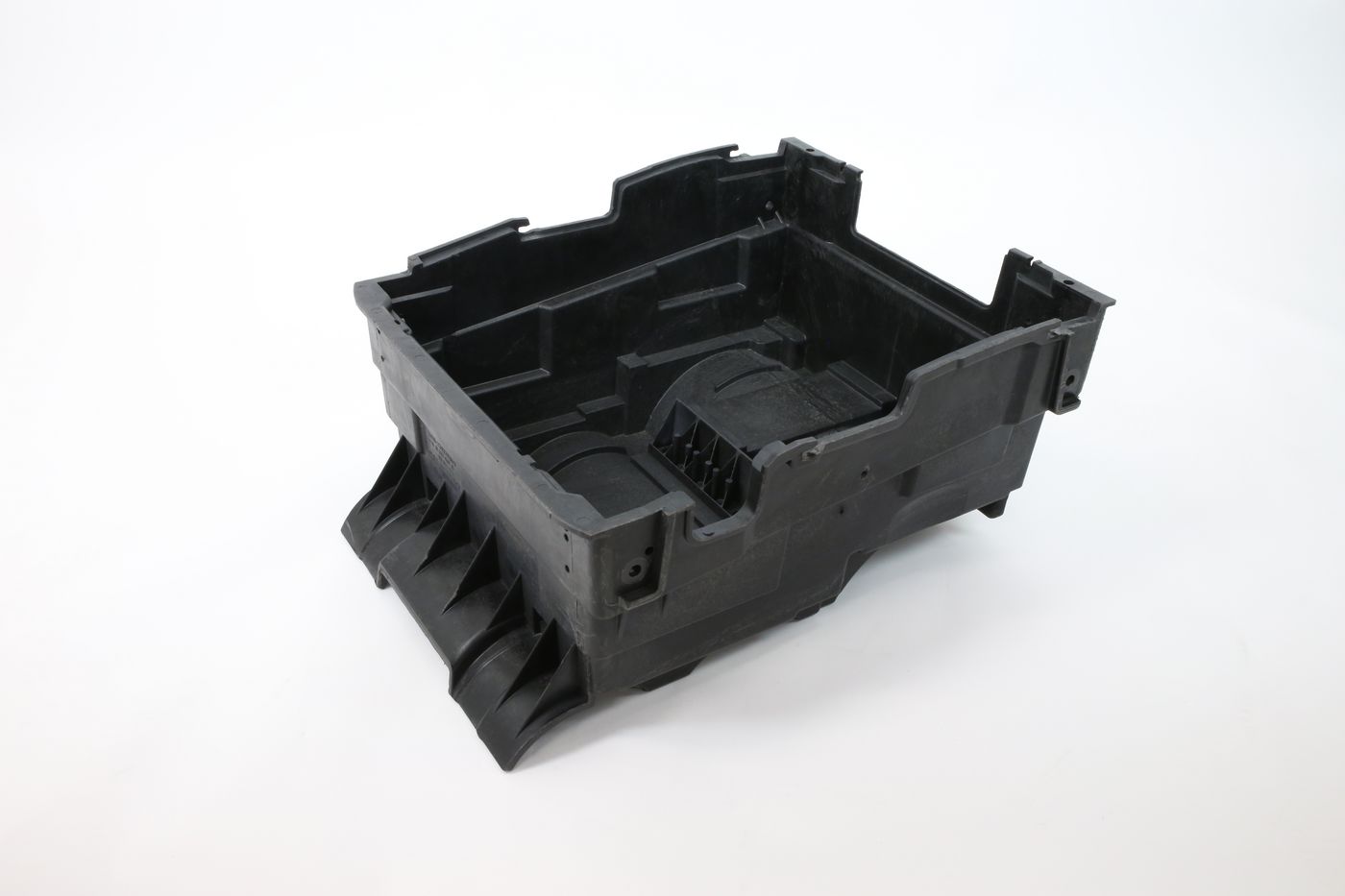
PRODUCT
STARROV® 490 / STARROV® 890 / TECHSPHERES / TECHBEADS
STARROV® 490: for D-LFT PP
STARROV® 890: for D-LFT PA
TECHSPHERES / TECHBEADS: Microglass balls with silane coupling agent
Glass fibers in form of rovings whose size is adapted to the respective compound are torn into the extruder and impregnated with the already melted matrix polymers. Whilst this they were shortened and then transferred into an injection ram. The continuous melting process assures steady material quality.
Compared with the LFT granulate the direct compounding in D-LFT is much more favourable because of no necessity of granulating and cooling as also glow energy- and material costs. Moreover the mechanical characteristics are essentially better by the lower fiber damage and only single melting phase.
ORGANO SHEETS
PROCESS
Organo sheets are plane semifinished products of a thermoplastic plastic matrix, which are reinforced with a fabric or multi layer fabric mostly out of glass fibers, what cares for a high mechanic strength of the component. Organo sheets are transformed to tridimensional parts by heating and then pressing in very short cycle times in a purely physical way – similar to the deep drawing of sheets, what explains the name „Organo sheet“.
MAIN ADVANTAGE
Thermoplastic structure components with function integration
ADVANTAGES
Defined rigidity, strength and heat expansion better than at the metallic patterns
High potential for the constructive shaping
Short cycle times similar to injection moulding
Full automatic production process
Components with end contour from the injection moulding tool (no necessity of rework)
CHARACTERISTICS
Thermoplastic components with defined continuous fiber reinforcement
Large weight saving potential without cuts in functionality
Fiber volume portion >50%
Production process highly to automate and to reproduce
High function integration possible
APPLICATION FIELDS
Frontends, seat shells and - backs, dashboards, floor groups, technical parts in the motor room, semifinished structure components
ANNUAL QUANTITIES
200.000 to 500.000 pieces
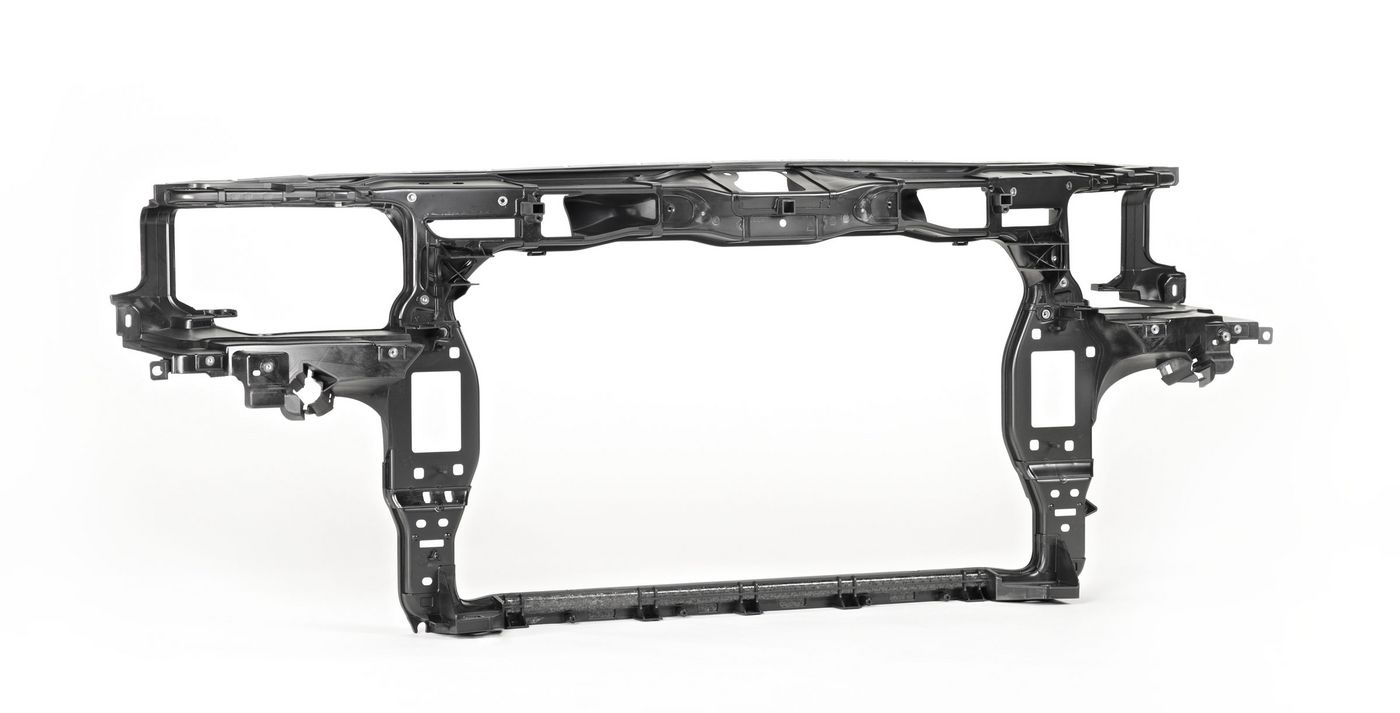
PRODUCT
HYBRID GLASS FIBER ROVING / FABRICS AND MULTI LAYER FABRICS OF HYBRID GLASS FIBERS / SEMIFINISHED PRODUCTS
HYBRID GLASS FIBER ROVING: with polypropylene matrix (PP)
FABRICS: of hybrid glass fibers according to client’s specification, also in UD
MULTI LAYER FABRICS: of hybrid glass fibers, uni- or multiaxial according to client’s request
SEMIFINISHED PRODUCTS: unidirectional with PP- and PE-matrix
Fabrics or multi layer fabrics of continuous fibers in thermoplastic matrix will be heated, transformed in the injection moulding tool and eventually relief-sprayed. So additional stiffenings can be realized by ribs and further functions can be integrated. The cycle times correspond to the common values with ca. 60 seconds and are determined essentially by the cooling phase in the tool.
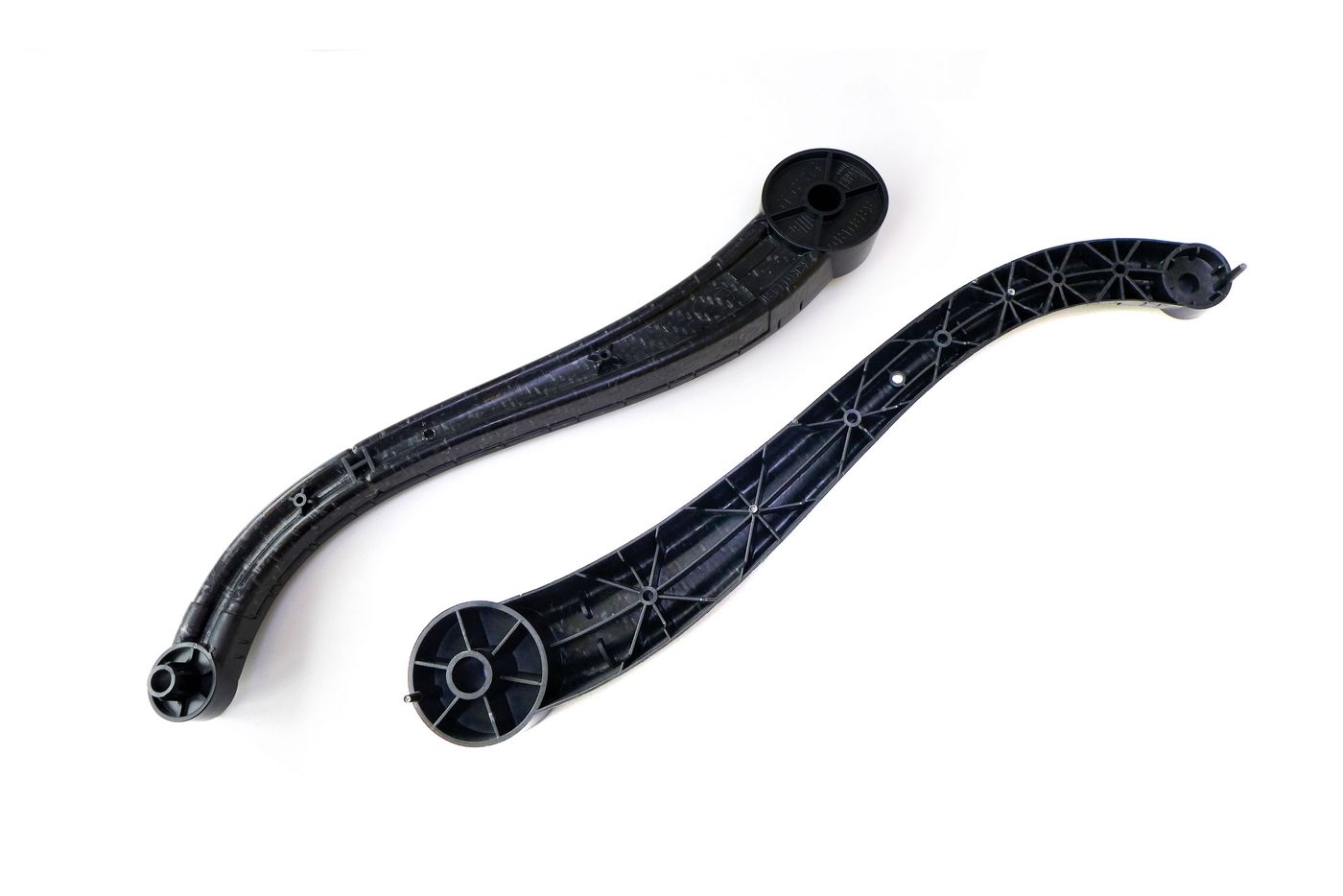